「伐採ってチェーンソーで伐り伐り倒すだけでしょ」――というほど簡単なものではありません。
木によって伸びている方向はバラバラで、それらを切り倒したい方向に確実に伐り倒すには高度なテクニックが要るのです。
安全のために、伐り込みの深さや角度などを定めた細かいルールもあります。また、倒れた木に当たったりチェーンソーに触れたりしてケガをする事故が最も起きやすく、特に気を遣う工程です。
木材供給の流れ
山から切り出してきた木は、いったいどのようにして建物になるのでしょう。
その大まかなプロセスは、次の「伐採」「運搬」「選別」「製材」「製品化」「施工」の6つに分けられます。
伐採
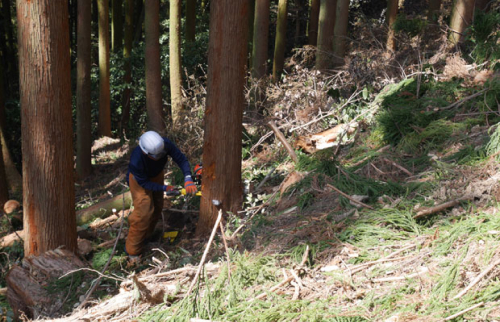
運搬
「運搬って、伐ってきた木を運ぶだけじゃないの?」――いえいえ、それほど単純ではありません。
確かに以前はきれいな木材をトラックに載せていくだけでしたが、最近では、細かい木くずやゆがんだ丸太などは、紙、燃料、合板の材料として使えます。
それらはわざわざ一緒に運ばず、ここで分けてしまいます。つまり捨ててしまうだけだともったいない木くずなどを「救出」する、大事な工程でもあるのです。
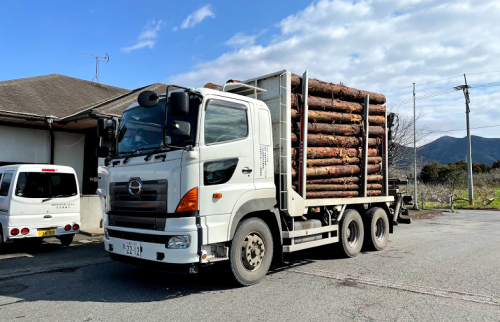
選別
「製材所に運び込んで、さあすぐに製材!」――というわけにはいかず、その前に、原木市場で長さや太さに応じて木材を分ける必要があります。
原木市場に運ばれた木材はまずベルトコンベヤーのような機械に載せて流し、長さや太さによって振り分けています。
作業は自動化されていますが、機械が大型なので、この振り分けの工程だけで大変な手間と経費が掛けられています。
その後、木材は競りにかけられ、製材工場などへ販売されます。
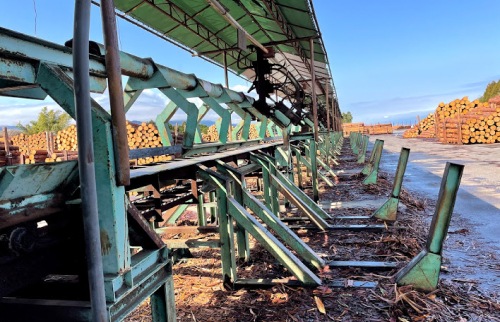
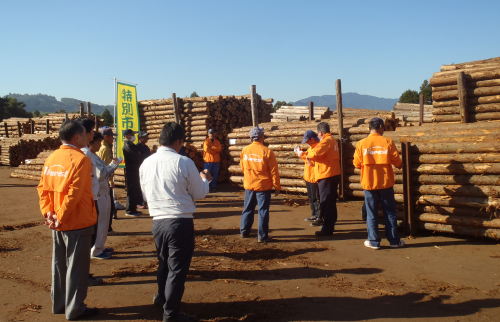
製材
選別された木材を製材工場で削ることで、ようやく角材や板材などができます。
ただ木材はもともと決して都合よくまっすぐに伸びてくれているわけではありません。
曲がっていたりへこんでいたりするものもたくさんあるので、鋸で角材としてまっすぐに切る必要があります。
以前は手作業で、作業員の経験と勘が求められていましたが、最近ではほとんど機械化され、刃先を0.01ミリ単位で調節して削りカスを少なくするなど、徹底して無駄を省く工夫をしています。
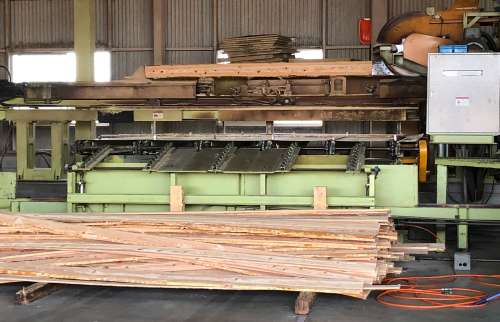
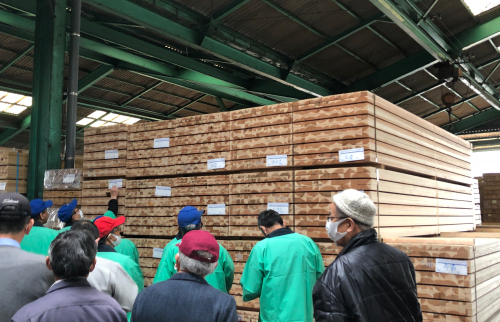
製品化
ニーズによって製材の段階で出荷される木材もありますが、この後に建築資材や部材としてさまざまな加工を施すものもあります。
また、自然のものを製品化するにあたり、乾燥や強度テストなどを行うことで、製品としての高い品質を保証するための努力が行われることがあります。

乾燥
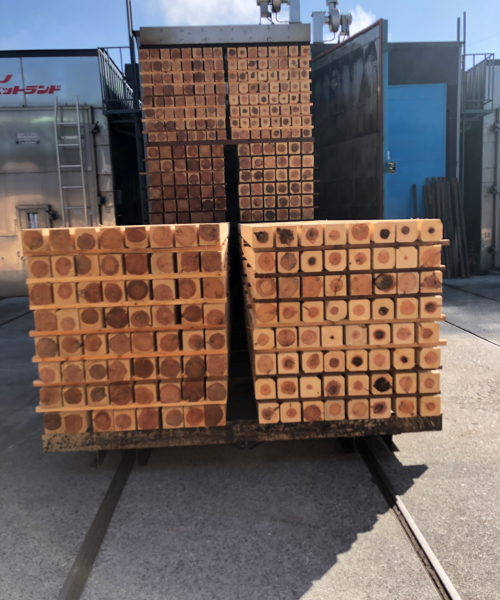
山から伐り出したばかりの丸太には水分がたくさん含まれていて、多いもので、完全に木を乾燥させきった時の重さと比べて約1.5倍もの量の水分が含まれています。
伐採後から少しずつ大気中に水分は蒸発していきますが、このまま製品化すると、水分と湿気によって木材が動いて、ゆがんだり縮んだりするので、大気中の湿度と同程度の水分量になり木材が環境に影響を受けづらくなるまで、あらかじめしっかりと乾燥させなければなりません。
自然に乾燥させると、種類によっては数か月から数年の長い時間がかかりますが、特殊な乾燥機に入れて人工的に乾燥させれば1週間程度まで短縮できます。

水分や強度のテスト
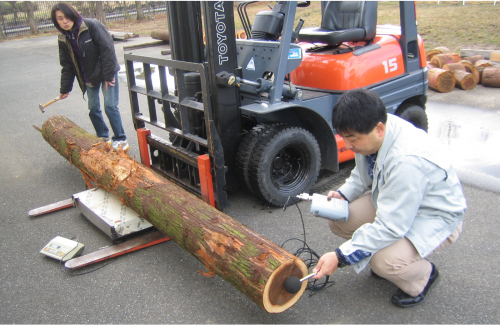
特に公共建築物をはじめとした一定の品質の保証が求められる場合などに、水分と強度のテストが行われる事があります。時間をかけて乾燥させた木材に木材水分計を当てるなどして、水分がきちんと一定の水準まで下がったかどうかを調べたり、木材をハンマーで打った音を測定し、周波数などから必要な強度が保たれているかどうかを調べたりします。いずれも木材を壊すことなく、一定の品質を満たしているかどうかのデータを取ることができます。

プレカット
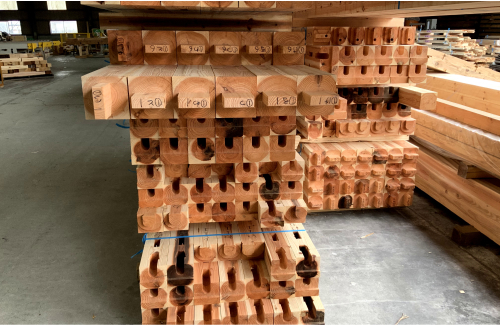
住宅用の木材の中には、建設現場に持っていく前に専用のプレカット工場に運び、あらかじめ現場で使う大きさに切ったり、接続するための金具をつけたりする「プレカット」を行うものがあります。
施工
製品化された木材がようやく建設現場に運ばれ、晴れて建物として生まれ変わります。
製品化までの工程の中で、様々な工夫や規格化・標準化の努力によって、近年では、工事の期間も数十年前よりも短くなっています。
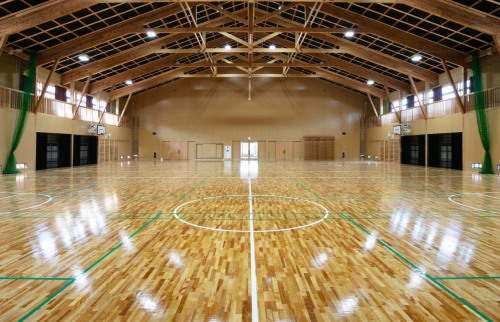